Risiken
Dynamik der Baugrube
Verschiedene Probleme wurden rechtzeitig erkannt und entschärft.
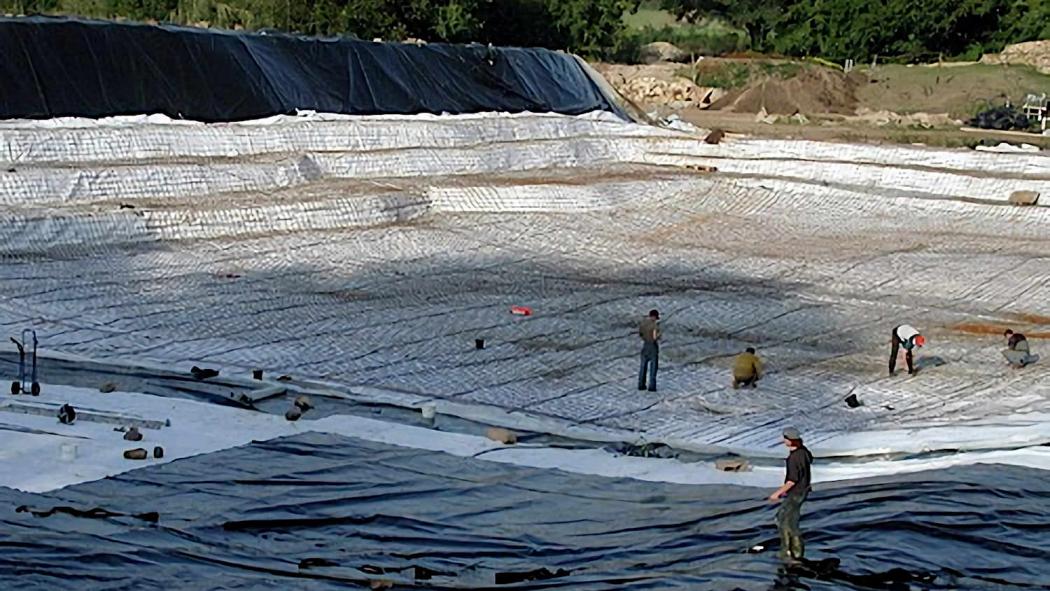
Der Unterwasserpark zählt technologisch zu den deutlich anspruchsvolleren Objekten. Die Baugrube war etwa 4 m unterhalb des Grundwasserspiegels ein völlig weicher Sandpudding, der erst mit etwa 2000 Tonnen Geröll und Schotter stabilisiert werden mußte.
Da Erde etwa doppelt so schwer wie Wasser ist, dürfte sich an der Gewichtsverteilung nach Anstau von etwa 7 m Wasser eigentlich nicht viel geändert haben.
Da Erde etwa doppelt so schwer wie Wasser ist, dürfte sich an der Gewichtsverteilung nach Anstau von etwa 7 m Wasser eigentlich nicht viel geändert haben.
Auch die Mauern innerhalb der Fläche haben zwar ein gewaltiges Gewicht, die Last ist jedoch durch die eingebaute Betonsohle so weit verteilt, daß diese etwa 16.000 Tonnen nur einer Erdschicht von etwa 1 m Höhe entsprechen.
Die abtransportierten restlichen ca. 3 m Erde müßten wir gewichtsmäßig durch 6 m Wasserstand ersetzen können. Die Gesamtgewichte dürften daher im Vergleich zur ursprünglichen Situation nur eher geringfügig anders sein.
Die abtransportierten restlichen ca. 3 m Erde müßten wir gewichtsmäßig durch 6 m Wasserstand ersetzen können. Die Gesamtgewichte dürften daher im Vergleich zur ursprünglichen Situation nur eher geringfügig anders sein.
Dennoch besteht ein Restrisiko durch die unvermeidliche Dynamik der Baugrube. Die Entlastung bei der Ausschachtung hat dazu geführt, daß sich der Boden etwas angehoben hat. Wir haben das zwar soweit stabilisiert, daß unser 23-Tonnen-Radlader keine Verformung mehr verursachte, dennoch pendelte die Sohle abhängig vom Grundwasserdruck bis zu 30 cm.
Der theoretisch ungünstigste Fall wäre ein Grundbruch, wie spontan mehrere in etwa 20 km Entfernung aufgetreten sind, als die Erdlast den weichen Untergrund eingedrückt hat. Dadurch sind z.T. mehrere Hektar große Seen (Heiliges Meer) entstanden. Da die geologischen Bedingungen hier etwas anders sind, ist das zwar unwahrscheinlich – wenn auch nicht ausgeschlossen.
Wir haben uns aus diesem Grund auch dazu entschlossen, die Dichtung von der Lastverteilung zu trennen. Wenn die Wasserlast nur auf die Betonsohle drücken würde, bestünde das Risiko, daß der Beton bricht und sich in die Folie drückt.
Aus diesem Grunde gibt es an verschiedenen Stellen Ventilationslöcher, die dafür sorgen, daß die Betonplatte im wesentlichen sich selbst und die Konstruktionen hält.
Aus diesem Grunde gibt es an verschiedenen Stellen Ventilationslöcher, die dafür sorgen, daß die Betonplatte im wesentlichen sich selbst und die Konstruktionen hält.
Die Wasserlast spielt keine Rolle, da der Druck oberhalb und unterhalb der Betonsohle gleich groß ist. Es ist sogar gut vorstellbar, daß sich zwischen Beton und Folie ein Hohlraum bildet, weil die Wasserlast größer ist als das Gewicht der Einbauten.
Was bleibt, ist das Risiko, daß die Folie an einer Stelle undicht ist oder wird. Wir haben das Risiko zunächst dadurch reduziert, daß wir zwei getrennte Folien eingebaut haben. Jede Naht wurde durch einen anderen Mitarbeiter kontrolliert. Für den unwahrscheinlichen Fall einer Beschädigung haben wir mehrere Vliesschichten eingebaut, von denen jede einzelne ausreichen würde, das Leckwasser aufzuhalten. Eingebautes Tonmehl würde dann an solche Leckstellen gespült und würde das Vlies verstopfen.
Für den unwahrscheinlichen Fall, daß dieser Selbstreparatur-Mechanismus nicht ausreicht, haben wir Leitungen eingebaut. Dadurch könnten wir gezielt zwischen die Folien und zwischen oberer Folie und deren Vliesabdeckung Tonminerale einpumpen, die etwaige Leckagen zuspülen würden.
Das größte Risiko während der Bauphase war ein rasch steigender Grundwasserstand. Besonders nach starken Regenfällen mußten wir mehrere hundert Kubikmeter pro Tag abpumpen, damit der Druck unter der Folie nicht zu stark wurde. In der Anfangsphase war es völlig problemlos, wenn die Betonplatte auf einer Fläche von einigen tausend Quadratmetern etwas angehoben wurde. Das System konnte so Hunderte von Kubikmetern speichern.
Das änderte sich mit fortschreitender Bautätigkeit. Durch das Gewicht der Einbauten wurde der Bereich, in dem sich die Betonplatte anheben konnte, zunehmend auf wenige hundert Quadratmeter reduziert – entsprechend gering wurde die Speicher-Reserve und die Vorwarnzeit.
Das änderte sich mit fortschreitender Bautätigkeit. Durch das Gewicht der Einbauten wurde der Bereich, in dem sich die Betonplatte anheben konnte, zunehmend auf wenige hundert Quadratmeter reduziert – entsprechend gering wurde die Speicher-Reserve und die Vorwarnzeit.
In der Schlussphase stand die Baustelle daher mehrfach ‚auf Messers Schneide‘. Hinzu kamen massive Stromausfälle im Dezember 2005. Benachbarte Teile des Münsterlandes waren tagelang von der Stromversorgung abgeschnitten. Die Unterbrechungen waren hier zwar immer nur kurz, ließen das Entwässerungs-System jedoch immer wieder kollabieren.
Dadurch traten einige Risse in der Betonplatte auf, die nachträglich noch einmal überbetoniert wurden. Das Ziel ist eine Begrenzung des Wasseraustausches, damit freigelegter Betonstahl im Bereich der Risse nicht übermäßig korrodiert.
Dadurch traten einige Risse in der Betonplatte auf, die nachträglich noch einmal überbetoniert wurden. Das Ziel ist eine Begrenzung des Wasseraustausches, damit freigelegter Betonstahl im Bereich der Risse nicht übermäßig korrodiert.
Der Bau des Unterwasserparks hat uns ganz wesentlich geholfen, Risiken auf Großbaustellen noch früher erkennen und bewerten zu können.
Verschiedene Probleme wurden rechtzeitig erkannt und entschärft. Andere waren nicht mehr zu korrigieren. Wir hätten z.B. die Sicherheitsreserven vor allem während der Bauphase noch deutlich steigern können. Die noch verbliebenen Risiken werden sich aber wahrscheinlich nicht nachteilig auswirken, weil in den Fällen die eingebauten Sicherheitsreserve greifen dürften.
Verschiedene Probleme wurden rechtzeitig erkannt und entschärft. Andere waren nicht mehr zu korrigieren. Wir hätten z.B. die Sicherheitsreserven vor allem während der Bauphase noch deutlich steigern können. Die noch verbliebenen Risiken werden sich aber wahrscheinlich nicht nachteilig auswirken, weil in den Fällen die eingebauten Sicherheitsreserve greifen dürften.
‚Hinterher ist man immer schlauer…‘, aber genau das ist aber auch das Ziel solcher Projekte: Man wächst mit den Anforderungen. Und aus Sicht der Kunden ist es sicherlich erwünscht, daß neue Bautechniken erst einmal firmenintern getestet werden und nicht am Kunden…
Damit stellt sich fast automatisch auch die Frage nach der Weiterverwertung des gewonnen Wissens. Dazu gibt es inzwischen verschiedene Anfragen – auch aus ganz anderen Kontinenten.
Wir werden sehen…
Damit stellt sich fast automatisch auch die Frage nach der Weiterverwertung des gewonnen Wissens. Dazu gibt es inzwischen verschiedene Anfragen – auch aus ganz anderen Kontinenten.
Wir werden sehen…